Tube manufacturing starts with selecting raw materials like steel and iron, then moves through heating, forming, and creating both seamless and welded tubes. Each step is tailored to ensure durability and precision. In this article, you’ll learn about every stage of the process and how these tubes are essential in industries like oil and gas.
Table of Contents
Raw Material Selection for Tube Manufacturing
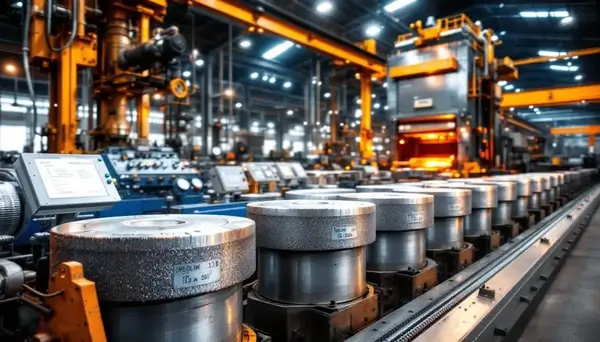
The journey of tube manufacturing begins with the careful selection of raw materials. The primary materials used are steel, iron, and carbon, chosen for their strength, durability, and versatility. These materials form the backbone of the tube manufacturing process, ensuring that the end products can withstand the demanding conditions they will face.
Additives like nickel and chromium are often included to enhance steel properties. These elements boost the strength and corrosion resistance of the steel, making it suitable for high-demand applications such as in the oil and gas industry. The right combination of additives can significantly improve the performance of the finished tubes, providing reliability in harsh environments.
Material quality is paramount in tube manufacturing. Pre-treatment processes like cleaning and surface treatment remove impurities and prepare the raw steel for manufacturing. These steps ensure that the steel can be formed and welded without defects, resulting in a higher-quality finished product.
Alloy steels are particularly valued in tube manufacturing for their enhanced strength and corrosion resistance. These materials are used in applications where standard steel would not suffice, such as in high-pressure environments or where exposure to corrosive substances is common. Meticulous preparation and selection of raw materials enable manufacturers to produce tubes that meet high standards of performance and durability.
Heating and Forming Steel
Once the raw materials are selected, the next step is heating and forming the steel. Steel must be heated to temperatures ranging from 2100-2400°F to achieve the necessary malleability for the rolling process. This intense heat transforms the raw steel into a more workable form, allowing it to be shaped into tubes with precision.
The rolling mill process forms steel into a cylindrical shape by passing heated steel through a series of rollers that gradually shape it. This process is repeated multiple times to ensure that the tube has a controlled wall thickness and an even outside diameter. The precision of the rolling mill process is crucial for producing high-quality tubes that meet exact specifications.
Heating not only achieves the right temperatures but also makes the steel malleable and workable during manufacturing. The heat treatment allows the steel to be shaped without cracking or breaking, ensuring the integrity of the final product. Careful control of heating and forming processes sets the stage for subsequent tube manufacturing steps.
From raw steel ingots to perfectly rolled pipes, the heating and forming stages are the foundation of the tube manufacturing process. These initial stages ensure that the steel is in the best possible condition for the intricate processes that follow, such as creating seamless and welded tubes.
Seamless Tube Production Process
Seamless tube production begins with heating steel billets. These billets are heated until they become white-hot, ready to be transformed into seamless pipes. Heated billets are formed into rounds under high pressure, creating the pipe’s initial shape.
The piercing process is a fascinating aspect of seamless steel pipe manufacturing. A bullet shaped piercer point creates a hole in the heated material, forming the pipe’s inner diameter. This step is crucial for achieving the seamless nature of the pipe, as it eliminates the need for welding and reduces potential weak points.
The mandrel mill process is another key component of seamless pipe production. This method involves elongating the pipe shell and shaping it to ensure controlled wall thickness and outside diameter. The quality of raw materials significantly influences the mechanical properties and performance of seamless steel pipes, making material selection crucial.
From piercing to final shaping, the seamless tube production process is designed to create pipes with superior mechanical strength and precision. These tubes are highly valued in industries where reliability and performance are paramount, such as in high-pressure applications in the oil and gas sector.
Welded Tubes: Types and Processes
Welded tubes are a staple in many industries, produced through a series of meticulous processes, we commonly see stainless steel tubes and carbon steel tubes. The journey begins with steel skelp, created by heating slabs to around 2,200°F. These slabs are then hot rolled into skelp, cut into flat sheets, and formed into cylindrical shapes. The width of the skelp determines the diameter of the resulting welded steel pipe, a critical factor in the manufacturing process.
Once the steel strip is rolled into a cylinder, the edges are welded together to form a solid tube. Sealing the edges through welding is crucial for ensuring the integrity and durability of the welded pipes. This process transforms flat pieces of steel into finished pipes, ready for various applications.
Hot billets are shaped into plates or strips and then welded to form pipes. The quality of the weld plays a significant role in the performance of the pipes, making it essential to choose the right welding method. The following subsections will delve into the different types of welding processes used in tube manufacturing, each with its unique advantages and applications.
Electric Resistance Welding (ERW)
Electric Resistance Welding (ERW) is widely used to produce welded steel pipes. It involves cold-forming a flat steel sheet into a cylinder and welding the edges with electrical current. The steel skelp is heated, rolled into a pipe shape, and then welded, resulting in a strong and durable pipe.
ERW pipes are known for their significant strength and durability, making them suitable for various applications. The process is efficient and cost-effective, providing a reliable option for producing high-quality welded pipes. Compared to other welding methods, ERW offers a balance of performance and economy, making it a popular choice in the industry.
High Frequency Induction Welding (HFI)
High Frequency Induction (HFI) welding shapes a continuous strip into an open pipe as it passes through high-frequency inductors, which induce a current for welding. The edges of the strip are heated through electrical resistance, allowing them to fuse together without additional filler material.
After the welding process, the HFI weld undergoes an annealing treatment to ensure that its properties are consistent with the surrounding base material. This step maintains the integrity and performance of the welded pipe.
The continuous pipe is straightened, sized, and cut to desired lengths using a flying saw. The HFI welding method is favored for its ability to produce pipes with precise tolerances and high manufacturing capacity. The process is efficient and produces strong welds capable of withstanding high fatigue and stress levels, significantly improving the quality of welded pipes.
Submerged Arc Welding (SAW)
Submerged Arc Welding (SAW) is particularly advantageous for creating large diameter tubes with high wall thickness. This technique involves using an electrical arc submerged in flux to weld steel plates together. The flux protects the weld from contamination and stabilizes the arc, resulting in a high-quality weld.
Longitudinal Submerged Arc Welded (LSAW) pipes are commonly used for larger diameter pipelines in critical applications, such as in the oil and gas industry. The SAW process ensures strong and reliable welds, capable of withstanding demanding conditions.
Tube Drawing and Sizing
Tube drawing and sizing are critical steps in achieving the desired dimensions and mechanical properties of the tubes. Tube drawing involves pulling the tube through a die to reduce its diameter and enhance mechanical properties through cold working. This process allows for precise control over the tube’s dimensions, ensuring that it meets the required specifications.
Mandrels play a crucial role in tube drawing, helping to maintain the tube’s shape and prevent deformities during resizing. Different methods of tube drawing, such as tube sinking, fixed plug drawing, and floating plug drawing, are used to meet specific production requirements. Each method offers unique advantages, making tube drawing a versatile technique in tube manufacturing, including the use of mandrel bars.
An oxalic and soap solution reduces friction during tube drawing. This coating helps the tubes slide through the dies more smoothly, reducing wear and tear on the equipment and improving the quality of the finished product.
The final tube drawing step involves pulling the tube over a drawing bench using die plugs. This step ensures that the tube achieves the desired shape and dimensions, ready for finishing and inspection.
Finishing and Inspection
After the tubes are drawn and sized, they undergo several finishing processes to ensure their quality and performance. These processes include cleaning, heat treatment, pickling, descaling, straightening, galvanizing, and marking. Each step prepares the tubes for final applications, ensuring they meet required standards.
Quality control inspections ensure steel pipes meet necessary standards. The inspections consist of hydrostatic testing and ultrasonic testing. Additionally, X-ray testing is also included. Non-destructive testing methods like ultrasonic and eddy current inspection identify internal and surface defects without damaging the pipes. These advanced technologies help detect any potential issues, ensuring the integrity and safety of the finished products.
The mechanical properties of steel pipes, including tensile strength and yield strength, are verified through standardized testing of samples. Quality control measures help ensure the integrity and safety of the finished products, reducing the risk of defects and ensuring that the tubes can withstand the demanding conditions they will face.
Applications in the Oil and Gas Industry
The oil and gas industry relies heavily on both seamless and welded pipes for various applications. Seamless pipes are favored for high-pressure applications due to their lack of weld seams and fewer stress points, providing superior mechanical strength and precision. These pipes are essential for transporting liquids and gases in demanding conditions, where reliability and performance are paramount.
Welded pipes, on the other hand, are cost-effective and suitable for lower pressure applications. They offer consistent wall thickness and shorter lead times, making them a practical choice for many projects. High Frequency Induction (HFI) welding creates stronger welds that withstand high fatigue and stress levels, significantly improving welded pipe quality.
The use of both seamless and welded pipes in the oil and gas industry highlights the versatility and importance of tube manufacturing. These pipes play a crucial role in ensuring the safe and efficient transport of vital resources, underpinning the industry’s infrastructure.
Summary
The process of tube manufacturing is a complex yet fascinating journey that begins with the careful selection of raw materials and involves multiple stages of heating, forming, welding, drawing, finishing, and inspection. Each step is meticulously executed to ensure the production of high-quality tubes that meet stringent standards and application requirements.
Understanding the intricacies of these processes not only highlights the engineering marvel behind tube manufacturing but also underscores the importance of quality control and precision. From seamless pipes used in high-pressure applications to welded pipes that offer cost-effective solutions, the variety of manufacturing methods ensures that there is a suitable product for every need. The reliability and performance of these tubes are critical, especially in industries such as oil and gas, where they play an indispensable role in infrastructure and resource transport.
Get the best Tube Manufacturing Equipment From New Victor
New Victor Tube Mills is a Chinese manufacturer of steel tubing machine, known for its superior quality High frequency pipe welding equipment.
Over the past 20 years we have provided professional and customized welded pipe solutions and perfectly functioning equipment to more than 500 companies all over the world. Make your business a success with the New Victor. Contact us today!