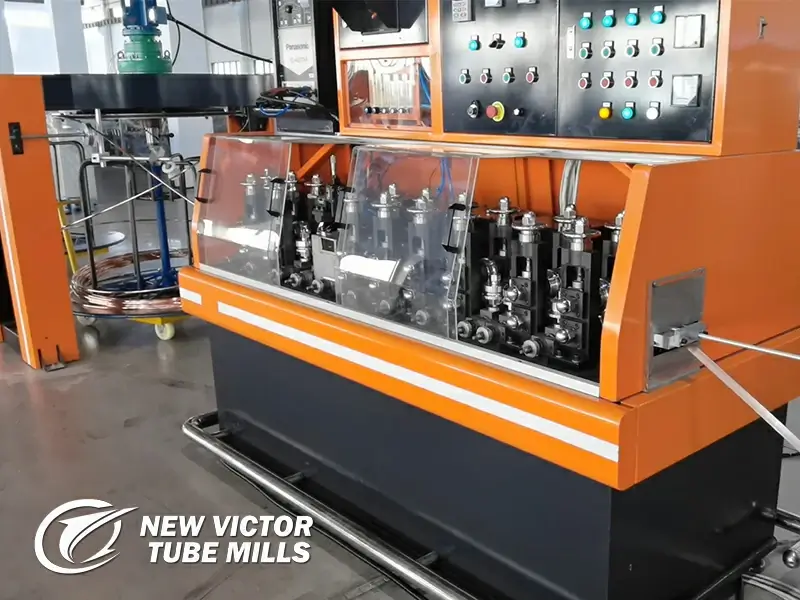
Copper clad aluminum machine is a class of industrial equipment specifically designed for the production of copper clad aluminum wire.
Copper clad aluminum wire is a kind of composite conductor material, using the light weight and cost advantage of aluminum, while combining the excellent conductive properties of copper, widely used in wire and cable, electronic components and other fields.
Process flow of Copper clad aluminum machine
The production process of copper clad aluminum involves several steps, mainly including raw material preparation → drawing → surface treatment → cladding (mechanical or thermal) → welding → straightening→ winding and packaging.
1. Preparation of raw materials
- Aluminum core material: usually use aluminum rod or aluminum wire, commonly pure aluminum or aluminum alloy (such as 1350 aluminum alloy).
- Copper cladding material: Usually high purity copper strip, copper foil or copper wire.
2. Aluminum wire drawing
- Aluminum rods or wires are drawn to the required diameter by means of a drawing machine.
3. Aluminum wire surface cleaning and treatment
- Use chemical or physical means to clean the surface of aluminum core, remove oxidation layer, oil and impurities, to ensure a close combination with the copper layer.
4. Copper cladding
- Copper cladding is the core step of the production process, the specific process can be divided into the following two ways:
- (1) Mechanical cladding: Using special cladding equipment, copper strips or foils are mechanically extruded onto the outer surface of the aluminum core to form a copper layer. After the copper tape is clad, it is usually necessary to weld the copper tape seams.
- (2) Thermal cladding: The copper is heated and melted, and then evenly coated on the surface of the aluminum core by spraying or flow coating.
This method requires high equipment and is suitable for producing high-precision copper-clad aluminum wires.
5. Welding
- After the copper strip is mechanically clad, its seams need to be sealed by welding.
Welding method: - High frequency welding: high efficiency, suitable for continuous production.
- Laser welding: high precision, suitable for high demand products.
- After welding, the seams need to be ground and polished to ensure a flat and flawless surface.
6. Straightening and shaping
- the copper clad aluminum wire is straightened by straightening machine to ensure the straightness and smooth surface of the wire.
- Strict dimensional checks are carried out during the sizing process to ensure that the diameter of the wire and the thickness of the copper layer are uniform.
7. Winding and Packaging
- Use the winding machine to wind up the completed copper clad aluminum wire, segment and weigh as required.
- Protective packaging of the wound products to avoid oxidation or mechanical damage during transportation and storage.